Pouring concrete in cold weather necessitates special attention and techniques to avoid a weak or flawed finish. This guide strips away the complexities, giving you succinct instructions on how to pour concrete in cold weather, maintaining the right temperature, choosing the correct mix, and protecting your work from the cold. With our hands-on advice, learn to navigate the cold like a pro and pour concrete that stands the test of time and temperature.
Key Takeaways
- Pouring concrete in cold weather presents unique challenges such as slowed chemical reactions and potential freezing, which can compromise the strength and durability of the structure if not properly managed.
- Pre-pour strategies are essential and include selecting the right concrete mix, pre-heating materials, and preparing the site, whereas post-pour practices like using insulating blankets and heated enclosures help maintain optimal curing temperatures.
- The use of additives and advanced technologies, such as calcium chloride or non-chloride admixtures, SmartRock sensors, and electric curing blankets, facilitate faster curing times and proper strength development in cold weather concreting.
Understanding Cold Weather Concreting Challenges
Pouring concrete in cold weather is no easy feat. As temperatures drop, the chemical reactions that strengthen the concrete slow down, potentially compromising the integrity of the structure. If concrete freezes before it’s fully cured, it can lose a significant amount of its strength, making it less durable and more susceptible to damage over time.
To have the concrete set properly, it’s necessary to maintain the correct temperatures throughout the curing process. Interestingly, concrete poured in cooler weather often results in a stronger end product due to the slow curing period. This makes it all the more important to avoid premature freezing during winter concrete projects to ensure the final product is as strong and durable as possible.
Pre-Pour Strategies for Concrete in Cold Climates
Certain strategies need to be implemented before pouring concrete in cold weather. These include choosing the right concrete mix and pre-heating materials to ensure better quality and strength. Adhering to these strategies, as recommended by the American Concrete Institute, will help prevent the concrete from freezing and ensure a successful pour.
Choosing the Right Concrete Mix
The process entails the crucial step of selecting the right concrete mix. Air-entrained concrete is essential for cold weather concreting as it contains microscopic air pockets which are crucial for resisting freeze-thaw cycles. These air bubbles are designed to prevent cracks and scaling, thus enhancing the durability and lifespan of the structure in a freezing climate.
However, while air-entrained concrete is more resistant to cold weather conditions, it can lead to a slight reduction in strength. To counteract this, it’s important to select a concrete mix with a minimum 4,000 psi compressive strength, ensuring the concrete can withstand harsh cold conditions and maintain its performance regardless of air temperature.
Keeping Materials Warm
Another key strategy in cold weather concreting is pre-heating materials. It’s essential to heat the water and aggregates to temperatures between 140˚F and 180˚F before mixing with cement. Using warm aggregates and water prevents the concrete from freezing and ensures the mix maintains the necessary temperatures for strength development.
Furthermore, preparing the site by removing ice, snow, and water is a key part of the process when pouring concrete in cold weather. This ensures that the site is ready for the pour, and helps avoid shocking the concrete, which could affect its strength and quality.
Protecting Freshly Poured Concrete from Freezing Temperatures
In cold weather concreting, safeguarding freshly poured concrete from freezing temperatures is vital, especially when working on frozen ground. This can be achieved by using heated enclosures and insulating blankets to maintain ideal curing conditions and prevent the concrete from freezing.
These techniques warrant a more detailed examination.
Utilizing Heated Enclosures
In cold weather concreting, heated enclosures offer a significant advantage. They combine insulation with even heat distribution, maintaining the ideal curing temperature range between 65°F and 85°F. Heated enclosures help maintain the activation energy required for proper hydration of concrete, ensuring that it cures correctly even in cold conditions.
These enclosures can be equipped with thermostats to regulate temperature, ensuring the concrete does not become too hot, which can be as detrimental as freezing. Furthermore, heating systems, such as hydronic systems, can provide efficient enclosure heating through the circulation of warm glycol and water, aiding in curing and minimizing downtime.
Applying Insulating Blankets
To protect freshly poured concrete from freezing temperatures, insulating blankets are of crucial importance. These blankets can provide both insulation and additional heating, ensuring the concrete temperature is maintained between 65°F and 85°F for proper curing. They also protect the concrete surface from the detrimental effects of rapid temperature fluctuations, which can lead to surface cracking.
To get the most out of these blankets, consider the following tips:
- Choose a blanket with a higher R-value, which indicates greater thermal resistance.
- Layer insulating blankets to enhance their insulating capacity, especially in extreme cold or when extended curing times are necessary.
- Ensure that the blankets are well-secured to prevent them from being blown away and exposing the concrete to potential freezing.
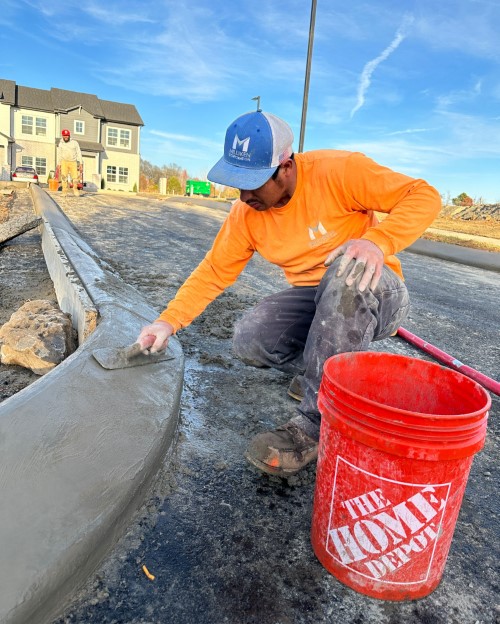
The Role of Additives in Cold Weather Concreting
In cold weather concreting, additives have a critical role. Accelerating admixtures, for instance, are specifically formulated to speed up setting time and protect against freezing in cold weather by boosting early strength gain. One such admixture is calcium chloride, which effectively accelerates concrete hydration and warms the mixture to improve workability in low temperatures.
Incorporating calcium chloride enables concrete to achieve its three-day strength in just one day and seven-day strength in three days, helping maintain construction schedules despite cold weather. However, when used with rebar within ICF walls, non-chloride admixtures are preferred for accelerating curing in cold conditions due to their compatibility and avoidance of rust and cracking unlike calcium chloride.
Monitoring and Maintaining Concrete Temperature
During the curing process in cold weather concreting, monitoring and maintaining the concrete temperature is crucial. Temperature control during this process is key for the strength, quality, and durability of the structure. Continuous monitoring of concrete temperature helps prevent:
- Early-age freezing
- Thermal shock
- Strength loss
- Cracking
Various tools and techniques can be used to monitor concrete temperature. For instance, the ASTM C1074 maturity method, used with sensors like SmartRock, estimates the in-place strength of concrete, aiding in decisions related to heating and project timelines. Dial pocket thermometers or infrared thermometers are also used to keep the temperature above 50°F (10°C) and prevent it from dropping below 40°F (4.5°C) in the first 24 hours.
Maintaining the concrete slab temperature during curing is necessary to maintain proper moisture content and temperature levels, allowing the concrete to reach its specific mix strength.
Post-Pour Care for Optimal Curing in Cold Weather
To ensure optimal curing in cold weather, post-pour care techniques need to be applied following the concrete pour. These include managing the exothermic reaction that occurs during the curing process and, if necessary, extending the curing time.
Managing the Exothermic Reaction
Being an exothermic reaction, the curing of concrete naturally generates heat. This heat is crucial for the curing process, and insulating blankets and ICF walls help retain it, aiding in the concrete curing process.
Temperature monitoring systems are crucial for using the temperature history to estimate in-place concrete strength, thereby optimizing curing procedures and ensuring the structural safety. By managing the exothermic reaction, we can ensure the curing process is not hindered by the cold weather conditions.
Extending Curing Time
To achieve in-place strength under cold weather conditions, it might be necessary to extend the concrete’s curing time. Under standard conditions, the protection period for curing concrete ranges from 1 to 6 days. However, concrete with accelerants and not under load may require shorter curing periods, while concrete without accelerants, under load, and exposed to cold in service needs longer protection periods during curing.
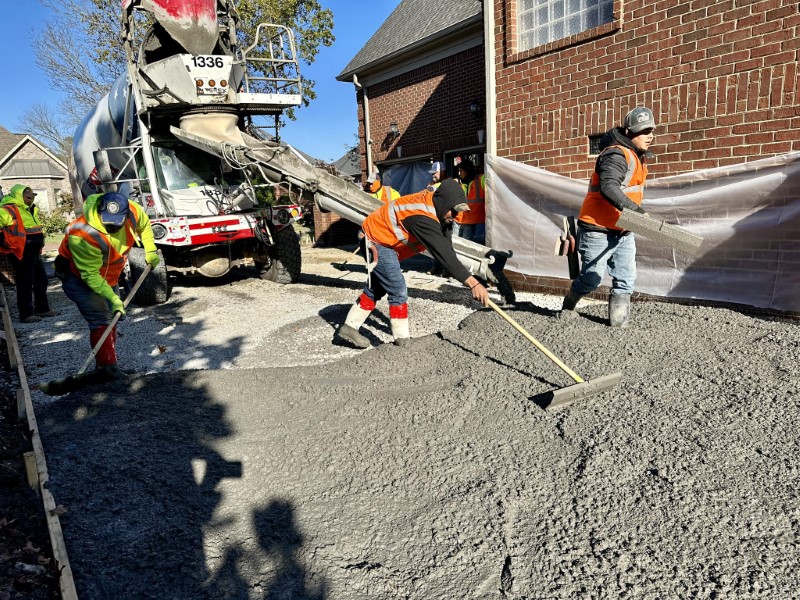
Best Practices for Worker Safety During Cold Weather Pours
During cold weather pours, worker safety is of utmost importance. Employers must adhere to OSHA’s cold stress guidelines to prevent cold-related injuries and illnesses. Workers should be adequately trained on recognizing the early signs of cold stress, prevention methods, and first aid treatment for cold-induced injuries.
Employers should provide engineering controls such as radiant heaters, shield work areas from wind, and implement safe work practices like warmed drinks and scheduling heavy work during the warmer parts of the day. Moreover, workers must be equipped with proper attire, including at least three layers of loose-fitting clothing that keeps moisture away, insulates, and shields from wind and rain, along with insulated waterproof gloves and boots.
Regular breaks in warm areas are also essential to prevent cold stress caused by cold temperatures, and having access to hot water can help maintain body warmth.
Adapting to Sudden Changes in Ambient Temperatures
Sudden changes in ambient temperatures, in addition to cold weather, can pose challenges during the pouring of concrete. To correctly pour concrete, it is crucial to consider factors such as unexpected rainfall, which can harm the finish and weaken the top layer of the concrete. In such cases, a float should be used to gently guide the water off the slab edges before beginning any finishing work.
Performing a scratch test can evaluate the surface integrity of the concrete if rain occurred after the initial set when the concrete has stiffened. This can help determine the potential for damage. If the rain causes recognizable damage such as dusting or surface scaling, it may be necessary to grind away the weakened layer and resurface, as long as the concrete beneath is still structurally sound.
Innovative Solutions: Insulated Concrete Forms (ICFs)
Innovative solutions like insulated concrete forms (ICFs) can offer substantial benefits in overcoming these challenges. ICFs maintain the heat generated during concrete’s curing process, adding strength as it cures. They also allow concrete placement in temperatures as low as -5° F (-15°C), reducing weather-related delays and extending the construction season.
High R-value ICFs like Fox Blocks exceed energy code requirements and reduce mechanical heating needs, offering energy efficiency and durability in cold climates. To ensure effective curing of ICF construction, exposed concrete at the top of walls can be insulated with high R-value thermal blankets or rigid foam boards like Halo’s Subterra.
Successfully Pour Concrete in the Coldest Months
Successful pouring of concrete in the coldest months can be achieved through careful planning, quick execution, and the use of electric concrete curing blankets. These blankets can cure concrete 2.8 times faster than conventional insulated blankets, which is essential to avoid delays due to cold weather and to ensure a strong final product.
Bear in mind, the strategies employed before, during, and after the pour heavily determine the success of pouring concrete in cold weather. From choosing the right concrete mix and pre-heating materials to monitoring concrete temperature and managing the exothermic reaction, every step is crucial.
Summary
In conclusion, pouring concrete in cold weather is indeed a challenging task, but with the right knowledge and techniques, it’s entirely feasible. From understanding the challenges to implementing pre-pour strategies, monitoring temperatures, managing the exothermic reaction, adapting to sudden weather changes, and using innovative solutions, every step plays a crucial role in the outcome. So, the next time you face the daunting task of pouring concrete in the coldest months, remember these tips, and you’re sure to succeed! Learn more about our concrete services here!
Frequently Asked Questions
What is the coldest temperature you can pour concrete?
The coldest temperature you can pour concrete in is 40 degrees Fahrenheit, as pouring concrete at or below freezing temperatures is generally not recommended due to the impact it can have on the hydration process.
Will concrete cure at 30 degrees?
Concrete will not cure properly at 30 degrees, as it needs to maintain a temperature of at least 40 degrees Fahrenheit for proper curing. Therefore, it is essential to monitor the concrete temperature during the curing process to ensure it meets this requirement.
Should you cover concrete with plastic in cold weather?
Yes, it is advisable to cover concrete with polyethylene sheeting or insulating blankets in cold weather to trap the heat generated during the exothermic curing process and prevent freezing within the first 24 hours after pouring.
How long does concrete take to cure in cold weather?
In cold weather, concrete takes about 48 hours to cure, during which it needs to be kept at temperatures between 50-60°F to reach optimal strength.
Can you pour concrete in the winter?
Yes, you can pour concrete in the winter by taking proper precautions, and it can even lead to stronger results due to the slow curing period.